In order for your business to always go in the right direction, you need to pay attention to the maintenance of your machinery. This way you will have lower operating costs and great benefits from the end results of your entire organization. All this is crucial for your business and the future of machinery. Although it is easier to let your equipment take care of itself, it will wear out and break down very quickly.
Then you can just discard and replace it or you will spend too much money on its repair which does not make too much sense. Instead, opt for regular maintenance, as it will bring you many more benefits. To help you make your equipment look its best, we’ve put together some helpful tips for you.
Maintenance goals
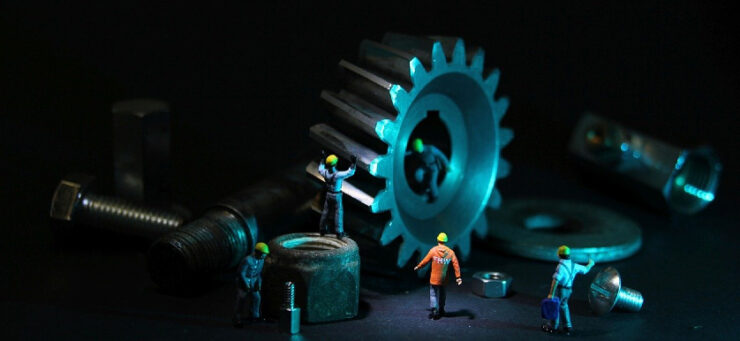
Before we move on to specific maintenance tips, we need to say a little more about the maintenance goals themselves. First of all, the most important thing is to ensure the conditions in which it is possible to reach the peak of productivity. In addition, these conditions should offer lower maintenance costs. Either way, this goal is achieved by breaking it down into smaller goals. For example, they relate to the maintenance of assets.
They must be in excellent condition, because that is the only way to increase the production capacity. It is also necessary to increase the chances of unplanned machine failures, shorten maintenance time, as well as the life of equipment and machines. The work environment must be safe for all and maintenance costs must be kept to a minimum. This will eliminate higher labor costs, loss of productivity due to machine failures, excessive wear of spare parts, etc.
Maintenance strategies
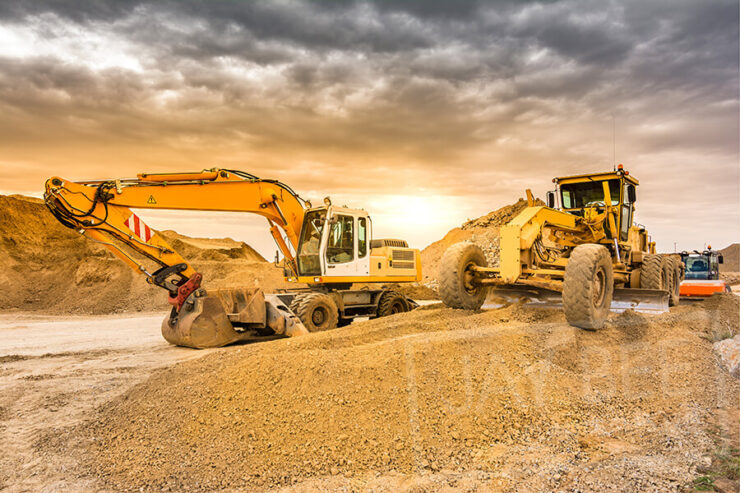
An appropriate strategy means finding the optimal solution. However, to achieve great success in preventive maintenance, you need to have the resources to invest in sensors for monitoring the condition and the like. It is also important to explore all the available options to decide on the ones that best suit your needs, but also your budget. Our advice is to consider several types of maintenance strategies instead of focusing solely on one. Since one object generally has several different means, each of them requires a different level of attention.
In that case, it will probably not pay off to apply one maintenance strategy for all of them. For example, decide on strategies using RCM analysis. It is an opportunity to discover which critical means require more attention, which should be maintained preventively or reactively. Of course, it is important to fully understand the requirements of each strategy, the needs of the facility and the available resources.
Get to know your machines
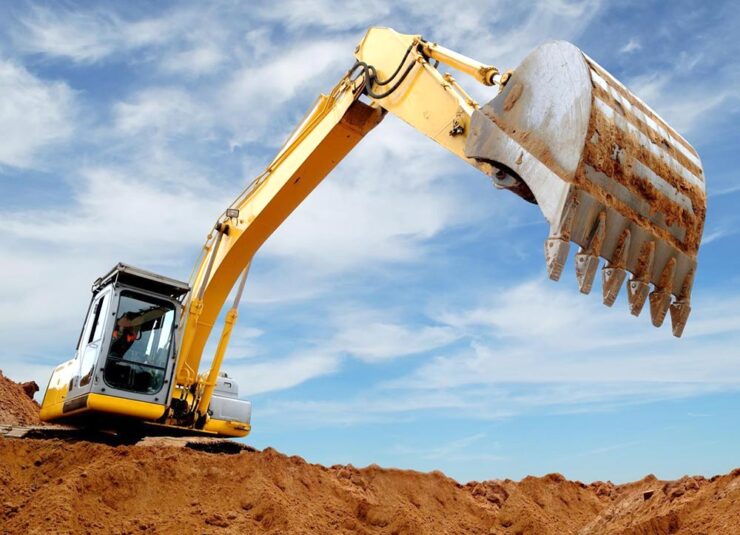
It is very important that you know your machines inside and out well. Based on a thorough knowledge, you will be able to assess which program is effective enough when it comes to preventive maintenance. All you need to find vital information is a machine equipment manual. So take the time to read and understand the equipment manual, as it contains detailed explanations of each component in the machine. They also prescribe maintenance steps and techniques, as well as other details such as items and flowcharts. This refers to the work that needs to be done if failures occur.
To get to know your machines better, you must always listen to your operators as well. They are a very important resource for getting to know the machine from the inside, because they always know when the machine is not as it should be and they will tell you that. Never doubt their contribution and always appreciate it, because it is a very wise strategy that you can make. Another wise move you can make is to know when to stop with operations. This refers to a situation where you suspect there is a problem. If you find yourself in this situation, stop working immediately. This will save you on failure costs and subsequent losses.
Employee training
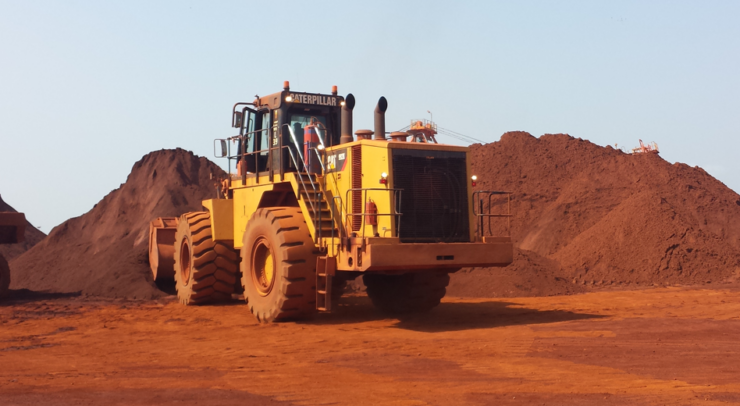
This is one of the most important factors when it comes to machine maintenance. People who manage them need to be trained enough to cause as little wear as possible, but also to be more productive. They will also have much more self-confidence, but will be equally confident in all other employees in their environment. Trained employees will respect their equipment, but will also know how to take proper care of them. This way you will save a lot of money on repairs and replacements. Our advice is to include this program in the basic programs, because preventive maintenance of machines is crucial for your business. It is not enough for employees to know how to start and shut down their machine.
Their task is to get to know her work on many higher levels. So, they need to perform routine, daily tasks without making a mistake. The training mainly consists of review of instructions, demonstration of the system and controls. With a program like this, they will gain enough skills and will be more confident in their work. It does not have to take long to give good results. It also doesn’t have to be complicated. It is important that communication is very clear when it comes to machine limitations, but also controls and systems for monitoring the operation of machines. Remember that only such workers can report the problem immediately, because they will assess it quickly and unmistakably.
What you should not do?
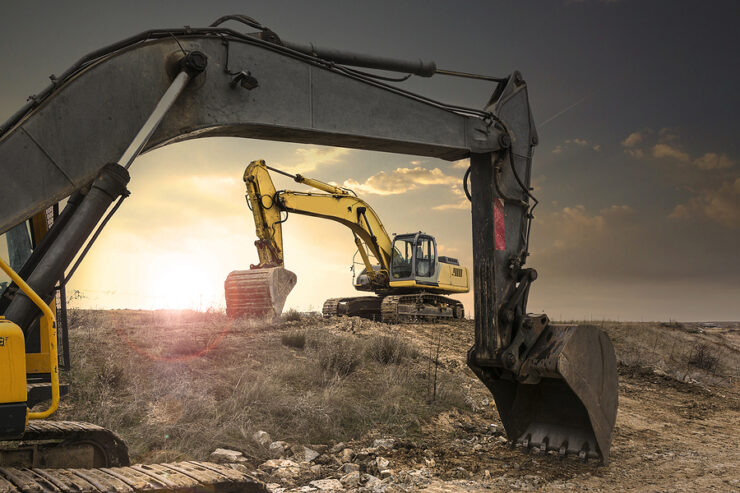
Equipment damage can also occur when something are spilled on the machine, and this often happens. Therefore, employees must not be negligent when it comes to this situation, which means that they must not bring drinks or other harmful substances near the machine. In addition, liquids can cause much bigger problems, such as those in electrical systems. You also have to respray plant machinery once in a while, to prevent corrosion, Otherwise, the metal may be damaged, which would quickly lead to the machine being unusable. Visit cpslift.com to find out more about resprays and refurbishment. Do not leave parts in the machine that do not work well enough. Everything that is not in good condition needs to be replaced, because much greater damage can occur, which is much more expensive than spare parts.
Conclusion
So, clean your machines properly and try to keep track of how it works. If you notice that a part is not working well, analyze the whole machine. Don’t forget the training program for workers, because only then will you be sure that they operate the machines properly. Always be honest with yourself when it comes to machine’s condition.